Wall to Wall
CO2 Revolution
We’ve been reducing CO2 emissions from the beginning.
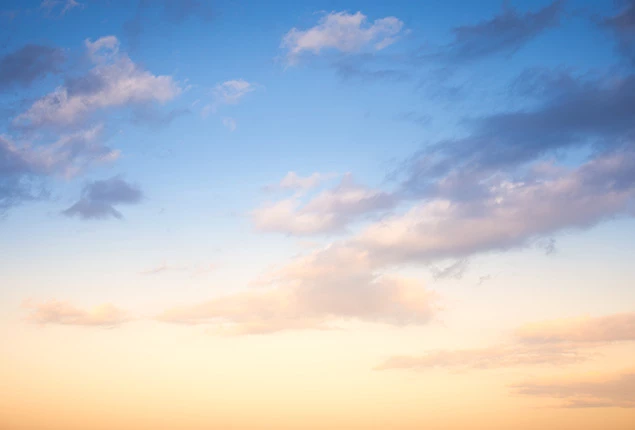
When it comes to sustainability, what people really want to know is what you are doing right now.
Shifting from remote packaging production to embedded, wall to wall manufacturing with Logoplaste makes an immediate impact … on our carbon footprint and the bottom line.
At Logoplaste we deliver mindful plastic packaging and we are doing this since 1976, when we created the embedded manufacturing business model, the wall to wall, where our plants are integrated with our clients’, allowing for bottles to flow seamlessly from production to filling.