Our Safety culture is our nº 1 priority
Everyone has to go home safe, every single day. We also promote Ethics & Integrity with a range of common global guidelines from our Corporate Values, Code of Conduct, Diversity & Inclusion and other relevant policies.
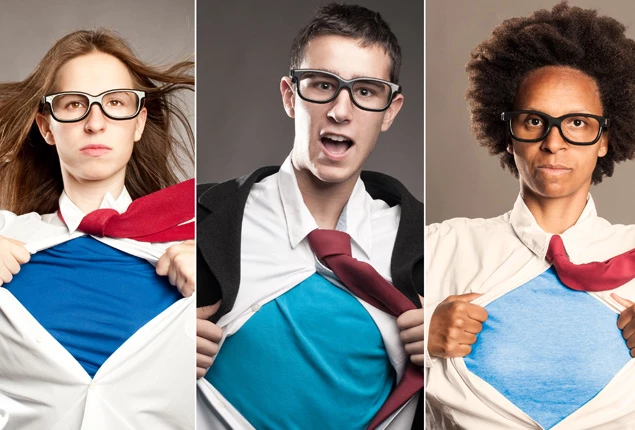
We believe in perfecting the art and science of rigid plastic packaging on 3 levels: with our teams and surrounding communities, creating a positive impact in the environment and relentlessly innovating
Everybody deserves to eave work, with not so much as a scratch. The San Luis team prevents accidents by working together and taking care of each other.
Our safety is our number one responsibility.
Andrés Medina
Plant Manager
Logoplaste San Luis Potosi, Mexico
At Logoplaste, we have a culture of continuous OHS improvement driven by four main strategies
The QEHS policy describes our vision and provides a framework for developing our management system. All sites share this policy with their teams and develop action plans.
Risk assessment identifies issues which are then analyzed by plant managers and their teams. Together, they develop and implement immediate action plans.
Each site holds regular meetings with all team members. The sessions address local performance, improvement plans, accidents, and potential changes in the workplace. Meeting minutes and action plans are posted. The use of unsafe conditions* reporting is key in employee engagement, enabling teams to identify hazards, making the workplace safer.
*An unsafe condition is anything with the potential to cause harm, injury and/or damage.
Training needs are clearly identified in the Global Training Matrix and all Logoplaste employees receive regular training suited to their role.
Training is delivered in the workplace during working hours whenever possible. Training effectiveness is measured through on-the-job tasks and simulations.